An Overview of Mold Materials
Mold material is most likely the most important aspect of the whole injection process as stated utilization essentially disrupts the durability of the mold, production cycle time or efficiency, and part quality of the product. Materials generally used in making molds include steel, aluminum, and various alloys. Each of these materials will offer meager benefits and numerous drawbacks.
The right material of the mold enables smooth production processes with a minimum of defects and less maintenance, hence ensuring long useful life. This material regulates the cooling rate and the cycle times and, therefore, as a direct implication, productivity and cost-effectiveness. A poorly reached material choice usually means frequent repairs, high changes in value, and problems related to the quality shortcomings.
Below we have discussed various materials for molds and analyzed properties so that you can understand how this would affect the different parts of injection molds and components. Now we shall make use of this characteristic in a material so as to enable you to make a rational decision in the optimization of production and hence translating to quality results in case you deal with manufacturing.
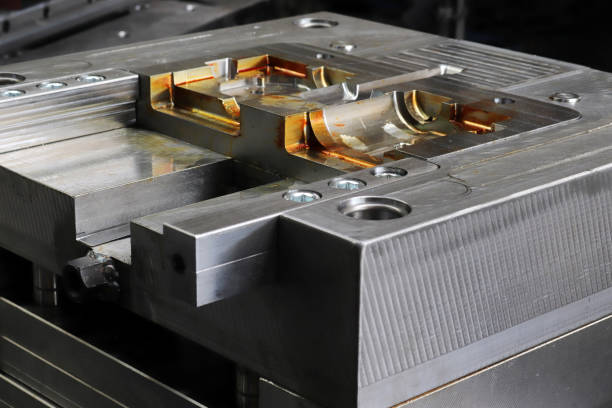
Injection Mold (Image Source: Istock)
Types of Mold Materials
Types of Mold Materials
There are many types of mold materials. These have different characteristics and thus have different applications. They include:
1. Steel
This is the most common mold material due to its strength and durability. Commonly used types include P20, H13, S7, and 420 Stainless.
P20: Good polishability and machinability, though not very tough—still used, though, because of low cost heat treatment; H13: Very good toughness and heat resistance; S7: Shock resistance; and 420 Stainless: Corrosion resistance.
2. Aluminum
Aluminum is also used as a substitute for steel because it is lightweight. Normally used grades are 7075 and QC-10. Molds of aluminum are quite easier to machine and offer faster cycle times.
However, in the case of steel molds, they are pretty weak, and they wear out very easily. They, however, can be effectively used in low to medium volume runs in production.
3. Beryllium Copper
This material gets high values of thermal conductivity as well as of strength. It is primarily used in areas of moulds where faster and directional dissipation of heat is required. This type of material is used for bringing about a significant reduction in cycle time as well as for improving the quality of the moulded parts.
4. Alloys
A combination of alloys can be used in the mold to enhance its performance. Alloys can be used that tend to provide a balance with increased strength, hardness, and thermal conductivity. Such types of materials are extensively used in order to fulfill some particular needs for molding and help elongate their service life.
5. Other Materials
Other materials in this category include nickel alloys, composites, and hybrid molds. Nickel alloys are used for their very good corrosion resistance and toughness. On the other hand, composites can offer a tailored mix of properties to answer specific needs.
A hybrid mold involves several materials, taking advantage of the unique characteristics of each to enhance performance and cost-effectiveness. The constituent materials are selected with explicit consideration of the uniqueness of the requirements of the whole injection molding process and the nature of the final product.
Properties of Mold Materials
Mold materials exhibit different properties, some of which include:
- Hardness
- Thermal Conductivity
- Corrosion Resistance
- Machinability
- Durability and Wear Resistance
1. Hardness
Hardness can be defined as the resistance of a material to deformation. This is important for maintaining the proper form of the mold material under high pressure. Steel is a hard material and aluminum is soft.
2. Thermal Conductivity
Thermal cycle impacts the time that the plastic part takes to cool in the mold. Faster cooling reduces the total time that a mold cycle takes, therefore enhancing the part’s quality. Copper-beryl shows greater thermal conduction in comparison to that of steel and aluminum. This also relies on alloy used.
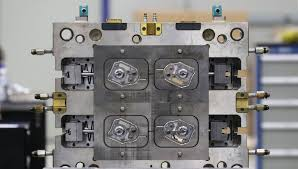
Steel Injection Mold (Image Source: Kaysun Corporation)
3. Corrosion Resistance
Corrosion resistance: It ensures the durability of the tools; it is not getting corroded with rust or with degradation of material. This is very important in cases where the tool is exposed to moisture or corrosive material. 420 Stainless steel, nickel alloys have very high machinability.
4. Machinability:
Which means how easily, therefore, a material can be easily cut and shaped, hence affecting the cost and time of making. Much-desired steel, P20, and aluminum for being highly machinable are mostly recommended along with an intricate plastic product design and rapid production.
5. Durability and Resistance to Wear
Thus, durability and wear resistance refer to the times a mold can last when entered into repeated use in a mold. High-wear applications require material that can withstand tremendous stresses over and over again. H13 tool steel and a few other alloys are made especially for great wear-and-tear resistance, which translates to the life of the mold.
It will be imperative, based on these properties, to select the appropriate mold material so that the best performance and quality of the molded part is maintained right from production through to the usage process.
Selection Criteria for Mold Materials
The considerations for selecting the right mold material have to be made keeping in mind the volume produced, the complexity of parts, the cycle, the cost, and the type of surface finish required. Efficient production, cost, and high ratio quality operation are all dramatically affected by each of the criteria.
Production Volume
One of the key factors in determining the selection of mold materials is production volume. Usually the choice in low-volume production situations is aluminum and similar types of materials because of the rather low acquisition cost and the fact that they machine easily. It is highly recommended that, for medium- to high-volume production runs, very highly resistant materials should be used, like P20 or H13 steel, since, after proper heat treatment, this strongly resists tolerance changes while keeping part properties over a good number of cycles.
Part Complexity
Part complexity also has a major impact on material choice. An intricate mold design that requires fine edge details calls for materials that do not distort when machined with good machinability. Aluminum and P20 steel are machinable materials that work well for this sort of detailed work. Very detailed parts that need to have features in highly complex geometries are possible because of their ability to mold very accurate internal features by using custom-shaped core pins produced from materials like beryllium copper.
Cycle Time
Cycle time includes duration taken for completion of one molding cycle, cooling included. The material in which the mold is made will determine the time it will take. Materials that have a high thermal conductivity, such as beryllium copper, cool the plastic at faster rates; therefore, cycle times are greatly reduced. The efficiency is important to high volume production processes because a reduction in cycle time will translate to important savings.
Cost Considerations
While choosing the mold material, one has to keep a trade-off between cost and mold performance, because aluminum is less costly and more easily machined; hence it becomes more fit for prototypes and low demands in productions. However, taking the example of a highly significant production quantity in its life cycle, the investment in some more durable, although costly, material, such as H13 steel, for instance, may be justified by the higher life expectancy and lesser expenses for maintenance service.
Surface finish requirement
The required surface finish of the final product also dictates material selection. Materials to the required degree of finish are those that can be polished to a high degree of finish. Some well-known materials for this are 420 Stainless steel and certain grades of aluminum. The material choice thereby influences the aesthetic as well as the functional quality of the molded parts.
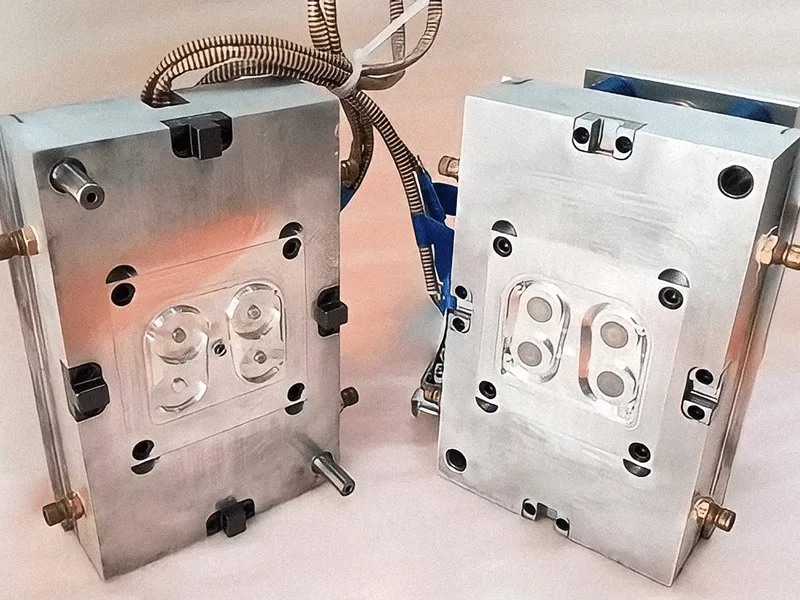
Injection Mold Components (Image Source: Seisa Medical)
Conclusion
There are many mold materials each with peculiar properties and advantages over the rest. Your choice is only dictated by the specific needs, goals and objectives, which have been prescribed to a project in your injection molding process. These are going to be placed into such factors as the volume production, part complexity, cycle time, its cost, and the surface finish requirements.