Inverters, Star-Delta, and Soft Starters: In industrial applications, controlling motor speed is crucial for efficient operation and energy savings. Devices like inverters, star-delta starters, and soft starters play a vital role in managing motor performance. This article explores where and why these devices are used, highlighting their differences and applications to help you choose the right solution for your needs. Understanding these tools can significantly enhance the safety and efficiency of your industrial processes.
Table of Contents
Where and Why is an Inverter Used?
An inverter, VFD, or drive is primarily used to control the speed of a load. For example, let’s say we have a conveyor belt that needs to rotate at a specific speed. Suppose it needs to rotate at 10m/minute, but sometimes at 5m/minute.
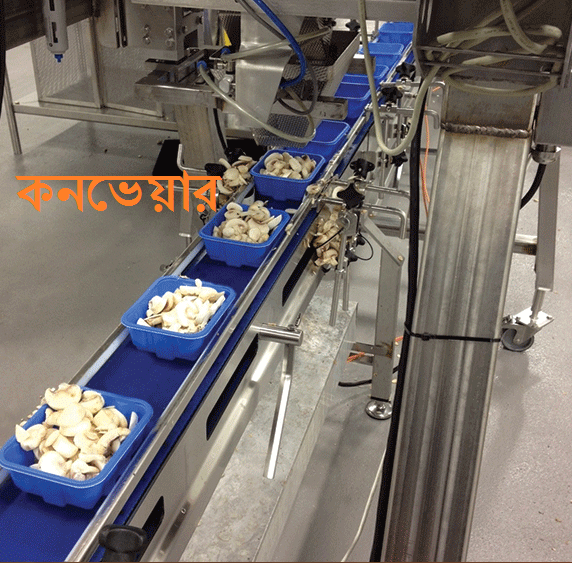
So how do we control the speed of this conveyor belt? We know that the conveyor belt is rotated with the help of a motor.
If we can control the motor’s speed, then the job is done. Inverters, VFDs, or drives are used to control the speed of the motor.
Using an inverter/VFD/drive, the motor’s load capacity can be increased or decreased. Suppose a motor can lift a maximum weight of 10 kg, but when the weight exceeds 5 kg, the motor will overload and shut down.
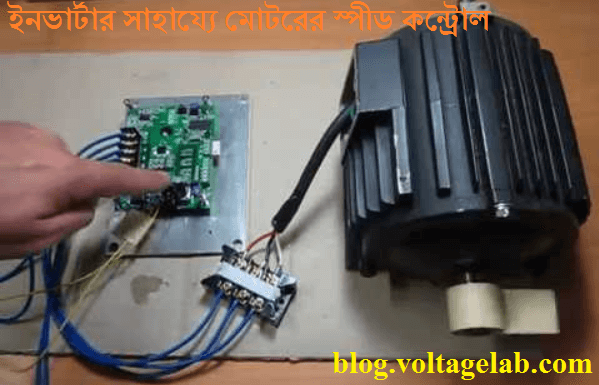
To do this, you can program the inverter to reduce the torque capacity. Using an inverter allows you to control the motor or load as needed, resulting in energy savings.
Where and Why is a Star-Delta Connection Used?
Suppose you have a large motor that requires a high starting torque. As a result, a large current is needed during startup. This condition will affect the overall power supply when the motor is running.
Additionally, if power consumption suddenly increases and then decreases rapidly, you can imagine the impact on the power supply, load, and devices 🙂
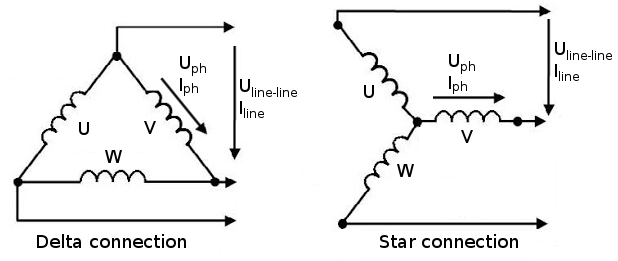
If the power supply is from a generator, the situation will worsen. To avoid such problems, the star-delta method is followed.
A delta connection requires less power compared to a star connection. For this reason, large loads are initially run in star mode for 3/5/6 seconds before switching to delta mode. Star-delta connections are never used for speed control.
However, if an inverter is used, there is no need for a star-delta connection. The inverter can be programmed to control the acceleration time (time to start) and de-acceleration time (time to stop) as needed. So, a star-delta connection is not required here.
Where and Why is a Soft Starter Used?
The soft starter works similarly to a star-delta connection. A soft starter is used to prevent large motors from having a negative impact on the overall system and power supply during startup. Its main function is to start the motor slowly according to the programmed settings, which is known as a soft start.
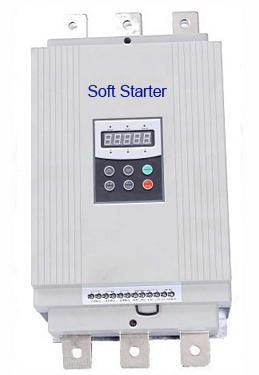
You might wonder, doesn’t an inverter do the same thing? However, there are some differences between an inverter/VFD/drive and a soft starter. A soft starter is primarily used where minimal speed control is required or where speed control is needed when the motor is running at full load.
But where constant speed control is required, an inverter, VFD, or drive is used.
Where the starting torque is low or medium, a soft starter is used, and where the starting torque is high, low, or medium, an inverter/VFD/drive is used.
What is the primary purpose of using an inverter or VFD in industrial applications?
The primary purpose of using an inverter or Variable Frequency Drive (VFD) is to control the speed of a motor, which in turn controls the speed of the connected load, such as a conveyor belt, ensuring precise operation and energy efficiency.
How does a star-delta starter help in motor starting?
A star-delta starter reduces the initial surge of current when starting large motors by initially running the motor in a star configuration to limit the power demand and then switching to delta for normal operation, protecting the overall power supply and connected devices.
When should a soft starter be used instead of an inverter or VFD?
A soft starter should be used in applications where the motor requires a gradual increase in speed during startup to prevent sudden power surges, especially when only slight speed control is needed during motor operation.
Can an inverter replace the need for a star-delta starter?
Yes, an inverter can replace the need for a star-delta starter, as it can be programmed to control the motor’s acceleration and deceleration times, eliminating the need for switching between star and delta configurations.
What are the differences between a soft starter and an inverter?
A soft starter gradually ramps up the motor’s speed at startup to protect the system from sudden power surges, while an inverter provides continuous speed control during motor operation, making it suitable for applications requiring precise and constant speed adjustments.