The delta connection is a fundamental wiring method used in three-phase electrical systems, particularly for connecting motors. In this configuration, the windings of the motor are connected in a triangular loop, allowing for efficient power distribution and enhanced motor performance. Delta connections are widely used in industrial applications due to their ability to handle high power loads and provide balanced voltage across the motor windings. In this article, we’ll explore the step-by-step process of connecting a motor in a delta configuration, how to verify the connection, the mathematical principles behind it, and the practical applications and benefits of using delta connections in motor operations.
When three coils, spaced 120 degrees apart, are connected in such a way that the end of the first coil is connected to the beginning of the second, the end of the second coil to the beginning of the third, and the end of the third coil to the beginning of the first, this connection is called a Delta Δ connection. It is also known as a Mesh connection.
Let’s see how to make a Delta connection step by step:
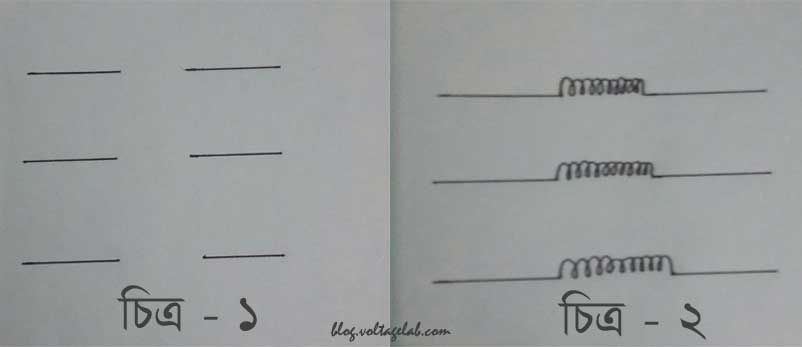
Figure 1: Three lines have been taken, and a gap is left in the middle of the lines.
Figure 2: Three coils have been drawn in the middle of the three lines.
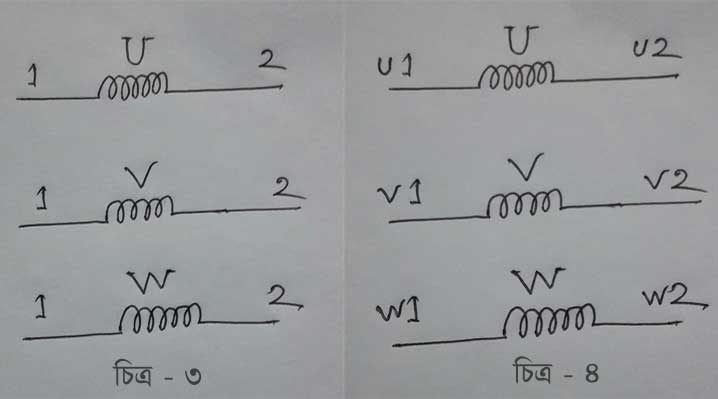
Figure 3: The three coils have been labeled as U, V, and W. Each coil’s starting and ending points are identified by numbers (start 1 and end 2).
Figure 4: The starting part of each coil is marked as U1, V1, W1, and the ending part as U2, V2, W2.
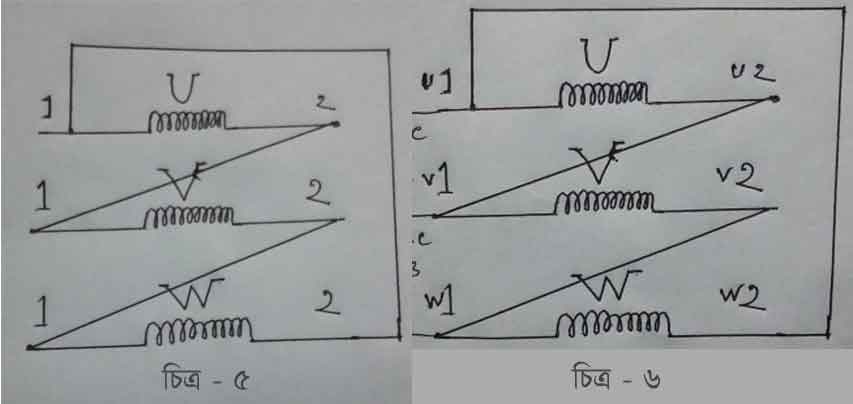
Figures 5 and 6: Figures 5 and 6 show the Delta connection diagram. Notice that the number 2 end of each coil is connected to the number 1 end of the next coil, i.e., (U2 V1), (V2 W1), (W2 U1) are connected.
Now let’s try to understand how to practically make a Delta connection. We know that six wires come out from the terminals of a three-phase motor. However, there are only three phases in the world, not six. Like all countries, Bangladesh also has only three phases.
The motor is connected using three wires from the PDB or REB line in the Delta method to run the motor.
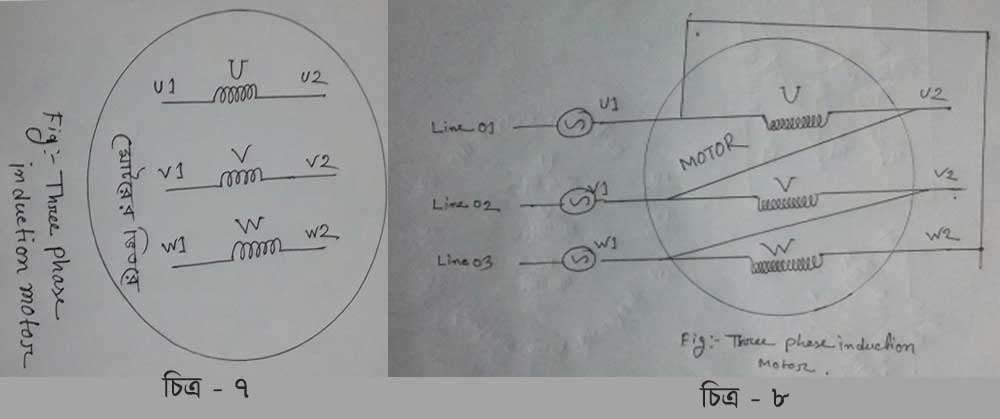
Figure 7 shows a motor, and Figure 8 shows the connection of the motor with a three-phase line. Note that the starting end of the first phase is named U1, the second phase V1, and the last phase W1. Similarly, the end of the motor’s phase is named U2, V2, and W2.
As shown in Figure 8, the motor is typically connected in Delta in this manner. It should be noted that heavy motors cannot be directly started in Delta; they may burn out. Therefore, the motor is initially run in Star for a few seconds before switching to Delta connection. This topic will be discussed in detail later.
Now compare the figure below with the textbook diagram.
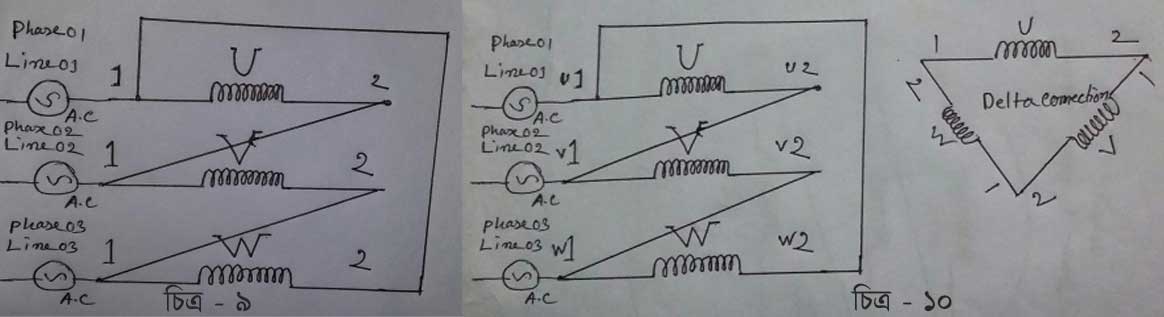
FAQ related to Connect a Motor Using Delta (Δ) Connection
1. How to connect a motor in a delta connection?
To connect a motor in a delta connection, connect the end of each phase winding to the beginning of the next phase. This forms a closed loop, creating a triangle-like connection, where each corner of the triangle represents a phase (U2 to V1, V2 to W1, W2 to U1).
2. How to check a delta connection motor?
To check a delta connection motor, use a multimeter to measure the resistance between the windings. Each winding should show a similar resistance, and there should be continuity between all three connections. If any winding is open or has significantly different resistance, the motor may be faulty.
3. What is the formula for delta connection in a motor?
In a delta connection, the line voltage (V_L) is equal to the phase voltage (V_P), and the line current (I_L) is √3 times the phase current (I_P). The formulas are:
VL=VPV_L = V_PVL=VP
IL=IP×3I_L = I_P \times \sqrt{3}IL=IP×3
4. How do I connect to an open delta connection?
In an open delta connection, only two transformers or windings are used instead of three. To connect to an open delta, connect two transformers in series to form a V-shaped configuration. This setup is often used when a full delta connection is not necessary.
5. Can a motor start with a delta connection?
While a motor can start with a delta connection, it’s typically not recommended for heavy motors. Starting directly in delta can cause a high inrush current, potentially damaging the motor. For large motors, it’s common to start in a star connection and then switch to delta once the motor is up to speed.
6. Why use star-delta connection in a motor?
The star-delta connection is used to reduce the starting current of the motor. In the star configuration, the voltage across each motor winding is reduced, resulting in lower current. Once the motor reaches a certain speed, it switches to a delta connection for full power operation.
7. How to calculate power in a delta connection?
In a delta connection, the power can be calculated using the formula:
P=3×VL×IL×Power FactorP = \sqrt{3} \times V_L \times I_L \times \text{Power Factor}P=3×VL×IL×Power Factor Where VLV_LVL is the line voltage, and ILI_LIL is the line current.
8. What is inside a delta connection?
Inside a delta connection, the three-phase windings of the motor are connected in a loop, forming a closed triangle. Each winding is connected end-to-start with the other windings, creating three junction points where the power supply phases are connected.