AC Motors are essential components in various applications, powering everything from household appliances to industrial machinery. This article explores the fundamentals of AC motors, including their types, working principles, and the key differences between single-phase and three-phase induction / ac motors. Understanding these basics will provide valuable insights into their operation and practical uses.
What is an AC Motor or Induction Motor?
Simply put, the induction motor’s stator has a three-phase winding. The poles created by this winding are always paired, such as 2 poles, 4 poles, 6 poles, etc.
A three-phase AC supply is given to the stator, resulting in current flow and the creation of a rotating magnetic field that rotates at synchronous speed and cuts the conductor inside the motor. This induces an EMF in the rotor conductor based on Faraday’s law of electromagnetic induction.
Due to the induced EMF, current flows through the rotor, generating rotation. As a result, the rotor starts rotating in the same direction as the magnetic field in the stator. Since this motor operates on the principle of induction, it is called an induction motor.
How many types of AC or Induction Motors are there?
Based on Supply
There are two types based on supply:
- Single-phase
- Three-phase
Single-phase Motor
Single-phase motors are further categorized as:
- Repulsion Motor
- Reluctance Motor
- Shaded Pole Motor
- Hysteresis Motor
- Universal Motor
- Capacitor Start and Capacitor Run Motor
- Standard Split Phase Motor
Three-phase Motor
Three-phase motors are of three types:
- Squirrel Cage Type
- Slip Ring Type
- Double Squirrel Cage Type
What is a Single-phase Induction Motor?
An induction motor where the stator is supplied with single-phase power and the rotor receives the required electrical energy through induction from the stator is called a single-phase induction motor.
Where is the Single-phase Induction Motor Used?
- In household water pumps
- In food and drink mixer machines
- In vacuum cleaners
How is a Single-phase Induction Motor Started?
- By splitting the phase of the motor
- By starting it as a repulsion motor
- By starting it as a capacitor motor
What is a Three-phase Induction Motor?
The stator of a three-phase induction motor has a three-phase winding. When supplied, it creates a rotating magnetic field that rotates at synchronous speed. This magnetic field induces voltage in the rotor conductor, producing current and torque.
Name Some Starting Methods for a Three-phase Induction Motor?
- Direct On Line Starter
- Three-phase Star-Delta Method
- Rotor Resistance Starter
- Auto Transformer Method
- Star Delta Starter
What is the Slip of an Induction Motor?
The rotor of an induction motor always rotates at a speed less than the synchronous speed. You might wonder why it rotates slower. If the rotor were to rotate at synchronous speed, the flux would not cut its conductor.
The difference between the synchronous speed (Ns) and rotor speed (Nr) divided by the synchronous speed, expressed as a percentage, is called the slip of the induction motor. It is usually between 4% to 8%.
%S = (Ns-Nr)*100/Ns
How to Reverse the Direction of a Three-phase Induction Motor?
To reverse the direction of a three-phase induction motor, interchange any two phases of the supply connection.
How to Control the Speed of an Induction Motor?
The speed of an induction motor can be controlled by:
- Reducing or increasing the supply voltage
- Changing the number of poles in the motor
- Varying the frequency
- Adjusting the rotor resistance
- Using the cascade control method
What is the Function of the Starter in an Induction Motor?
Sometimes, it is necessary to reduce the voltage during starting to keep the starting current within a safe limit. Additionally, to increase the starting torque, extra resistance may be needed, which is typically handled by the starter.
Now, you might wonder why the starting current exceeds the safe limit. When the motor is supplied, initially, there is no back EMF, so the motor is directly connected to the line, drawing a current that is 5 to 7 times higher than normal.
Why Can’t a Single-phase Motor Start on Its Own?
A single-phase motor cannot start on its own because it lacks torque. Why is there no torque? We know that the single-phase motor’s supply is directly given to the winding, creating a magnetic field in the motor.
As a result, the motor moves in one direction during the first half-cycle and in the opposite direction during the next half-cycle, making the net torque over a complete cycle zero.
What Are the Advantages and Disadvantages of Induction Motors?
Advantages
- Very simple construction, making them sturdy and long-lasting
- High efficiency, and no need for brushes during operation
- Low frictional losses, and they work efficiently with a high power factor
- Relatively cheap and highly reliable
- Low maintenance cost, and no need for a DC exciter
Disadvantages
- Speed control issues
- Speed decreases with increased load
- Low starting torque
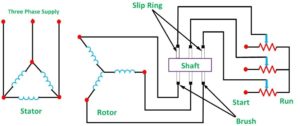
Power Stages of an Induction Motor
Input ⇒ Stator Input ⇒ Copper and Core Loss ⇒ Rotor Input ⇒ Rotor Copper and Core Loss ⇒ Friction and Windage Loss ⇒ Output Power at Shaft
Why Is an Induction Motor Called an Asynchronous Motor?
In simple terms, the speed at which an induction motor rotates is less than the synchronous speed, which is why it is called an asynchronous motor. Its slip usually ranges from 2% to 5% of the synchronous speed.
What Does 80% Power Factor in an Induction Motor Mean?
An 80% power factor in an induction motor means that the motor’s real power is 80% of its apparent power, i.e., (Real Power/Apparent Power)*100 = 80%.
What is Starting Torque and Running Torque?
Starting Torque
The torque required to move a motor’s rotor from a standstill is called starting torque.
Running Torque
The torque required to keep the motor rotating at its rated speed is called running torque.
Conclusion
In this article, we have provided some important MCQs and answers on induction motors. We hope these questions will be helpful for everyone. Thank you!